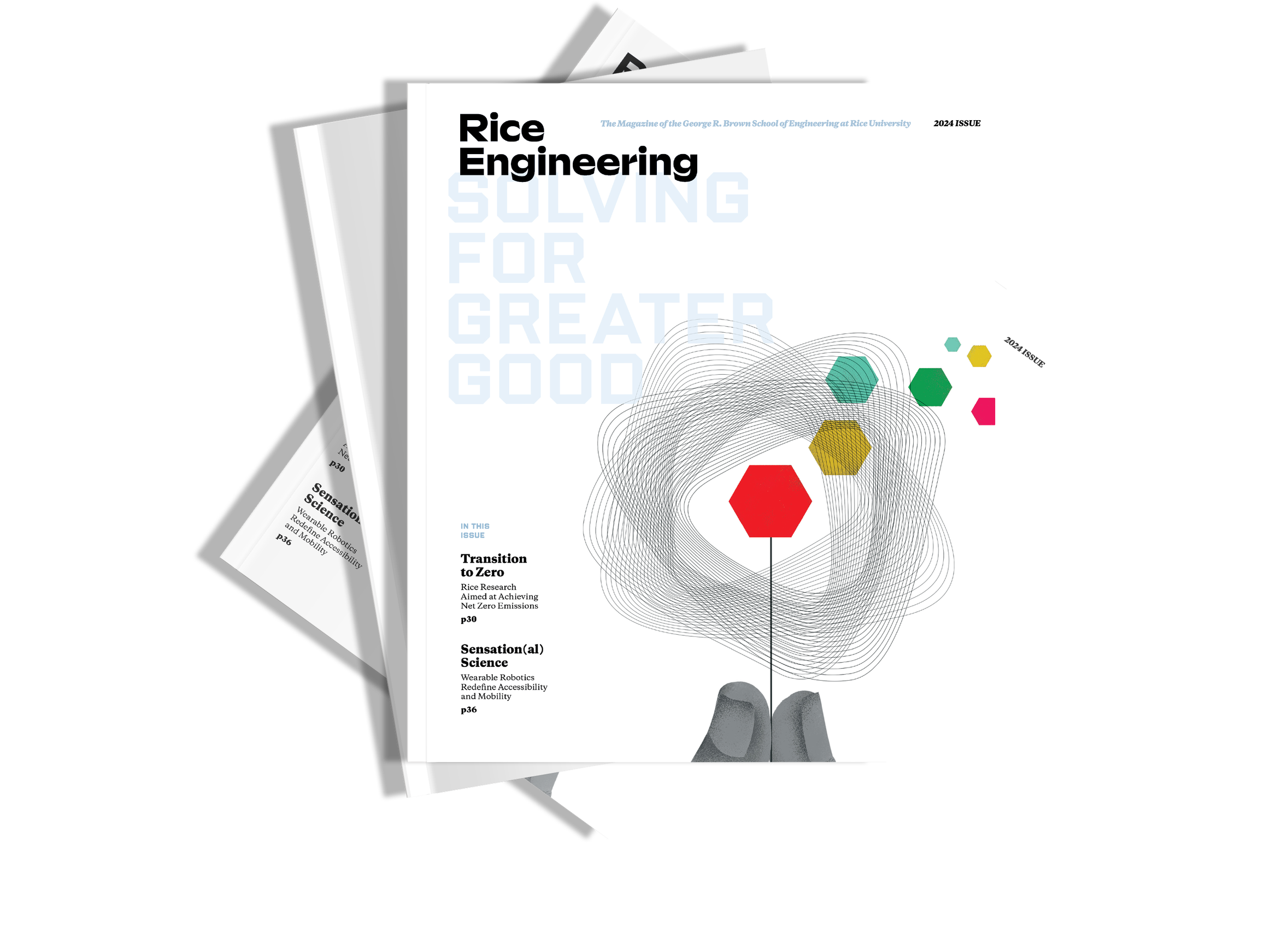
The spring 2024 issue of Rice Engineering Magazine is here!
At Rice Engineering, we are driven by a passion for innovation and a commitment to responsible engineering practices. It’s with great excitement that we unveil the new design of Rice Engineering magazine, which underscores our dedication to excellence in research, education, and service. The 2023-24 issue is full of news about how Rice Engineering is solving for greater good.
Wearable, textile-based device taps into sense of touch
In the popular imagination, a robot is still a clanking metal humanoid likely to be a threat to humans. Researchers at Rice are dispelling that dated misconception and turning robots into wearable devices for disabled and elderly patients, and even the able-bodied.

published in Device
“Our lab focuses on human-robot applications for rehabilitation, training and virtual reality. We develop robotic systems — hardware and control algorithms — to use in upper extremity rehabilitation after people have suffered a stroke or spinal cord injury. We make devices for wearable haptic feedback that also have applications in virtual reality and prosthetics,” said Marcia O’Malley, Thomas Michael Panos Family Professor in Mechanical Engineering and director of the Mechatronics and Haptic Interfaces Lab.
“Haptic” refers to the sense of touch, a resource increasingly used in robotics development. It includes tactile sensations conveyed through the skin and kinesthetic sensations from muscles and tendons. They enable us to continually sense the relative positions and movements of our bodies without conscious effort and are critical for efficient performance by robots.
“My focus is haptic work,” O’Malley said. “When we say ‘wearable,’ we refer to a device conforming to the human body. It can take many forms — clothing, rings, a bracelet, a watch.”
Among O’Malley’s collaborators is Daniel Preston, assistant professor of mechanical engineering and director of the Preston Innovation Laboratory.
“We’re optimistic about the future,” Preston said. “For instance, it’s important that we eliminate tethers and large, bulky power sources, so people can have easier mobility. We want to make and store energy from the act of walking itself and even capture body heat. The ideas are endless.”
In collaboration, the O’Malley and Preston labs have recently developed a wearable, textile-based device that helps patients compensate for visual and auditory losses. Such technology reduces the dependence on hardware by programming haptic cues into the textile structure of wearables, using fluidic controls.
“Traditional control systems use voltage and current, meaning you’d need many electronic inputs to achieve complex haptic cues,” Preston said. “In this device, we’ve offloaded much of that complexity to the fluidic controller and require only a small number of electronic inputs to provide sophisticated haptic stimulation.”
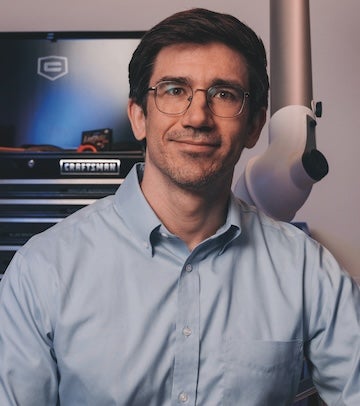
The new wearable consists of a belt and textile sleeves, and relies on fluidic signals such as pressures and flow rates to control delivery of haptic cues, including vibration, tapping and squeezing. A lightweight carbon dioxide tank or small electronic air pump worn on the belt feeds airtight circuits incorporated into the heat-sealable textiles, causing small pouches, as many as six on each sleeve, to inflate with varying force and frequency.
The device was successfully tested for real-world navigation on a one-mile route through the streets of Houston. In the future, it could be modified to incorporate other sensing and control mechanisms, and permit users with vision or hearing loss to detect obstacles and navigate their movements.
The technology also holds promise for restoring the sense of touch for amputees by embedding sensors on a prosthesis to gather data the wearables could relay as haptic feedback elsewhere on the body.
“The haptic feedback felt by the user would be directly correlated with the actions they’re taking,” O’Malley said. “One of the big advantages of using these smart textiles for haptic devices is that they bring a lot more freedom and flexibility to the design space. We’re no longer constrained by the size or shape of components that need to be incorporated into a design.”
“Our goal is to make robots that collaborate better with humans,” Preston said.